DAYTON, Ohio — The futuristic Next Generation Air Dominance fighter platform now in the works is likely to be one of the most complex, highest-stakes weapon acquisitions in the U.S. Air Force’s history.
The sixth-generation fighter jet is expected to include new technologies ranging from cutting-edge adaptive engines to an autonomous drone flying alongside its wings. If NGAD works as the service hopes, it could prove critical in a potential war against China.
But in recent years, the advanced digital engineering techniques the Air Force once thought would lead to a revolution in rapid aircraft development and fielding have not always panned out. The concept allows engineers to create designs or models to test assumptions more quickly and accurately. And with digital engineering expected to play a central role in the NGAD effort, experts say the service will have to ensure the technique lives up to its promise.
This isn’t the first time the Air Force looked to a digital design revolution to usher in a new generation of aircraft. During the service’s last major new jet acquisition, the T-7A Red Hawk trainer, the Air Force and manufacturer Boeing promised the program would lead to a fresh way of designing and building future aircraft.
The service was so bullish on the potential benefits of a future built on digital aircraft engineering that in 2020 it made a short-lived attempt to rebrand the trainer the “eT-7,” and also dub future aircraft designed in this way with an “e” prefix.
Since then, a series of missteps and delays have pushed back key milestones on the T-7 — and caused a bit of the shine to rub off from its much-heralded digital design approach.
In a May breakfast, Air Force Secretary Frank Kendall made clear the extent to which digital engineering had lost its luster in the wake of the T-7′s troubles.
“It is a significant improvement, but it has been overhyped,” Kendall told reporters. “More integrated digital designs, better modeling all help, but they’re not revolutionary. … They don’t replace testing entirely.”
‘Not a magic wand’
Digital engineering has been around in one form or another since the 1970s, said Heather Penney, a senior resident fellow at the Mitchell Institute for Aerospace Studies. Computer-aided design helped shape many aircraft in use today, including the B-2 Spirit stealth bomber, F-22 Raptor jet and F-35 Joint Strike Fighter.
The concept evolved as processing, algorithms, modeling and simulation improved, she explained. Now, Penney said, digital engineering can include everything from 3D models of individual aircraft parts — fuel pumps, hydraulic lines, electrical system bundles and more — to models of how an aircraft’s various systems interact with one another or the aircraft as a whole.
Having this type of digital model doesn’t only inform the aircraft’s design, she said, but also shapes the tooling and manufacturing of the aircraft. As an example of a significant advancement this technology can provide, she pointed to Boeing’s “amazing” ability to use digital processes to fabricate T-7 components so accurately that they fit together without needing shims. And she highlighted the B-21 and the LGM-35A Sentinel intercontinental ballistic missile as examples of complex and so-far successful Air Force acquisitions that made tremendous use of digital engineering.
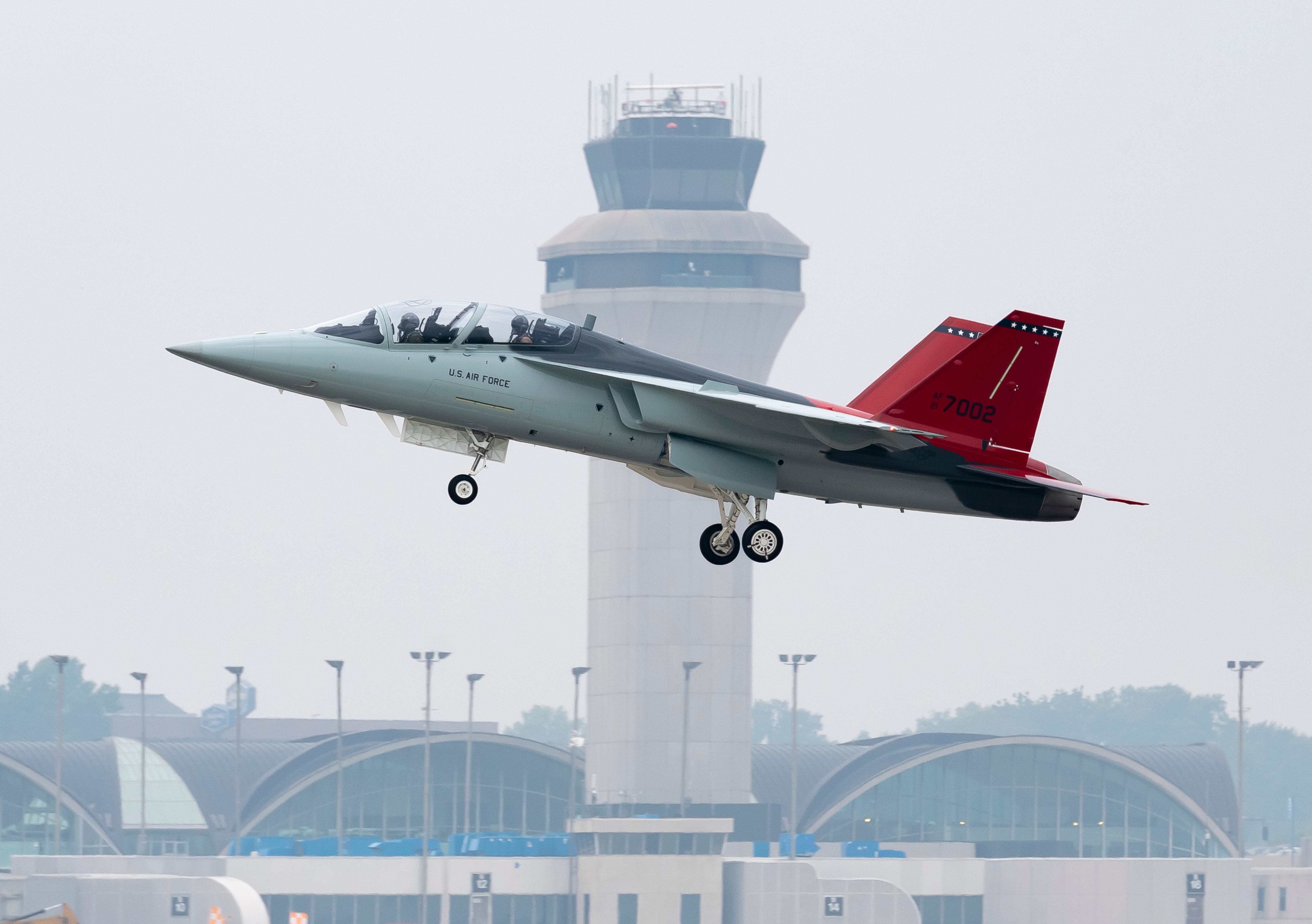
But, she noted, “it’s not a magic wand that waves away any bumps [in] design,” and can’t take the place of solid engineering fundamentals.
An aerodynamic instability in the T-7 known as “wing rock,” in which its wings could have dangerously rocked back-and-forth in some flight conditions, was fixed in 2021, but was one of several factors that prompted the Air Force and Boeing to start to rethink its schedule in 2022.
Additional issues, including an escape system and ejection seat that could endanger the T-7′s pilots, as well as glitches with its flight control software, led to further delays.
For “the eT-7, digital engineering was going to make this airplane go fast, the design was going to go fast, it was going to knit everybody together, it was going to be a bumpless design process,” Penney said. “What our experience with the eT-7 has been is that digital engineering is just a tool. You still have to get the engineering right.”
Penney said blame for the T-7′s problems, like those with its ejection seat system, can’t be laid at the feet of digital engineering — but notably, digital modeling failed to catch the T-7′s issues in advance.
In roundtables with reporters at the Air Force’s Life Cycle Industry Days, held July 31-Aug. 1 in Ohio, officials described how the service is trying to expand its approach to digital engineering by spreading the benefits throughout the entire life span of an aircraft — in a concept it calls digital materiel management.
In a June whitepaper, Air Force Materiel Command said digital materiel management aims to dramatically accelerate and streamline the processes of designing, creating and sustaining aircraft or other systems by using digital methods throughout their life cycles, from the initial idea to retirement.
“We’re playing the long game,” said Brig. Gen. Dale White, the Air Force’s program executive officer for fighters and advanced aircraft. “That is critically important. If you just look at digital through the lens of design and development and test, you’re going to limit yourself. We all know the majority of the funding is spent on the sustainment tail.”
“And so being able to make decisions that you couldn’t normally make before, because you didn’t have that amount of information this early in the process, really is a game changer,” continued White, who oversees the NGAD program.
By having a single digital trail following an aircraft through its entire life cycle, officials argue, it will be easier to carry out techniques such as predictive maintenance, which helps track exactly how long parts have been on a plane and leads to their replacement before they are likely to fail.
Certainly, the concept can work, but the Government Accountability Office found in a December 2022 report that the military hasn’t taken full advantage of it. Technology limitations are hampering widespread adoption of predictive maintenance, such as problems with older information systems and a lack of digitized maintenance manuals.
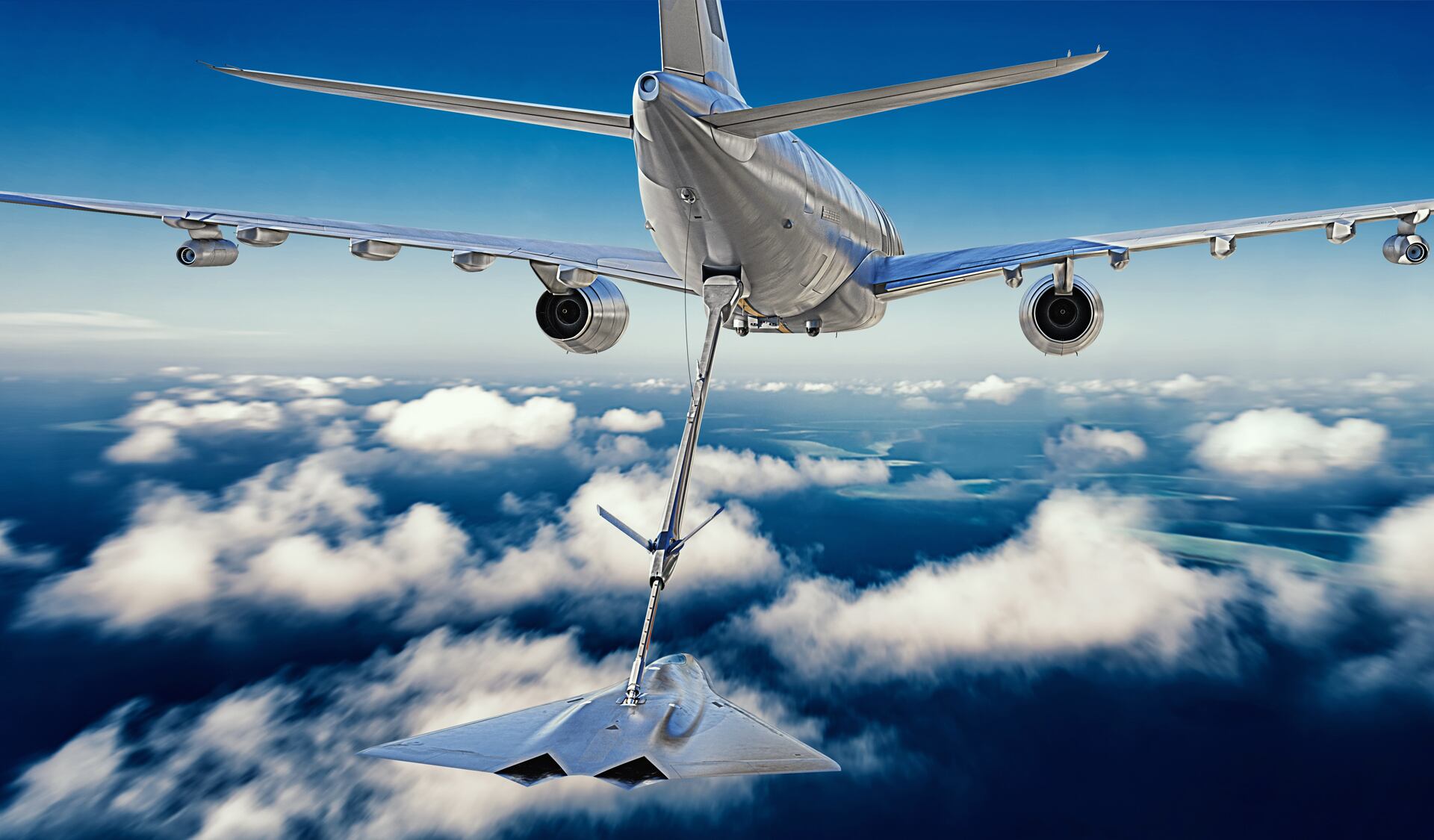
The military reported “predictive maintenance has enabled pilots to avoid helicopter aircraft accidents and identify failures that were undetected by mechanics, avoid maintenance costs, and redirect maintenance personnel to other work creating cost efficiencies,” GAO said in the report. But “the examples are from limited experience. [And] in order to implement predictive maintenance more broadly, changes will be necessary to mainstream business processes to address resource challenges from personnel, parts, and technology.”
“According to military service officials, unplanned maintenance — which adversely affects costs and operations — can be reduced through greater use of predictive maintenance,” the report read. “Military service officials acknowledge that, while they have examples of improvements they attribute to predictive maintenance implementation, the examples are from limited experience, and the military services generally lack metrics to evaluate the results of predictive maintenance.”
Next-gen propulsion
In May, the Air Force took its most significant public step forward to date on NGAD when it announced it had sent industry a classified solicitation for an engineering and manufacturing development contract for the secretive program. The Air Force also said it plans to award the contract in 2024, with Lockheed Martin and Boeing widely expected to be the two remaining bidders. The Air Force hopes to have NGAD in production by the end of this decade.
And with Kendall estimating each fighter’s price tag at hundreds of millions of dollars, the service can’t afford to get it wrong.
So far, little has been said about how digital engineering is contributing to NGAD. During the May roundtable, a few days after the Air Force’s solicitation announcement, Kendall described a situation where service engineers and other NGAD program officials at Wright-Patterson Air Force Base in Ohio were “living in the same design space as the bidders.” Program officials have direct access to the databases that the two firms vying for the program use to hone their NGAD designs, Kendall said, and use that access to offer their own suggestions.
In Dayton, Ohio, White — who oversees the creation of NGAD — and other officials offered more insight into how the Air Force and contractors are using digital engineering as they ramp up work designing the aircraft and propulsion systems.
When past fighters were designed, White explained, they were sketched out on paper in two dimensions. As the designs went through one iteration after another, he said, those sheets multiplied until reams of paper tracing each step in an aircraft’s evolution piled up.
But as NGAD takes shape, White said, those mountains of paper have been replaced by a constantly evolving digital design. In years and even decades to come, he added, that will make it easier for NGAD to evolve to stay ahead of the threats it will face.

“It’s a living thing,” he said. “You can constantly make informed decisions about where you’re going and where you think you need to be. … It’s not enough to be digital just from an engineering perspective. You’ve got to have a good foundation to understand what the threat is doing. And that’s going to allow us greater flexibility.”
“What it’s allowing us to do is become more informed buyers,” he added. “In this world, there are a lot of things you don’t have to do physically because you have greater visibility and a better grasp and command of the knowledge because of the digital [tools] we didn’t have before.”
And the NGAD’s propulsion system will be the first entirely new military propulsion system to be digitally designed and produced, according to John Sneden, director of the Air Force’s propulsion directorate.
The companies working on the Next Generation Adaptive Propulsion system, or NGAP — primarily GE Aerospace and Pratt & Whitney, alongside Lockheed Martin, Boeing and Northrop Grumman — are just now getting into a place where they can start designing it in a completely digital, 3D environment, he said. Given the last fighter engines designed for the Air Force were created decades ago for the F-35 and F-22, Sneden said, this is a new approach.
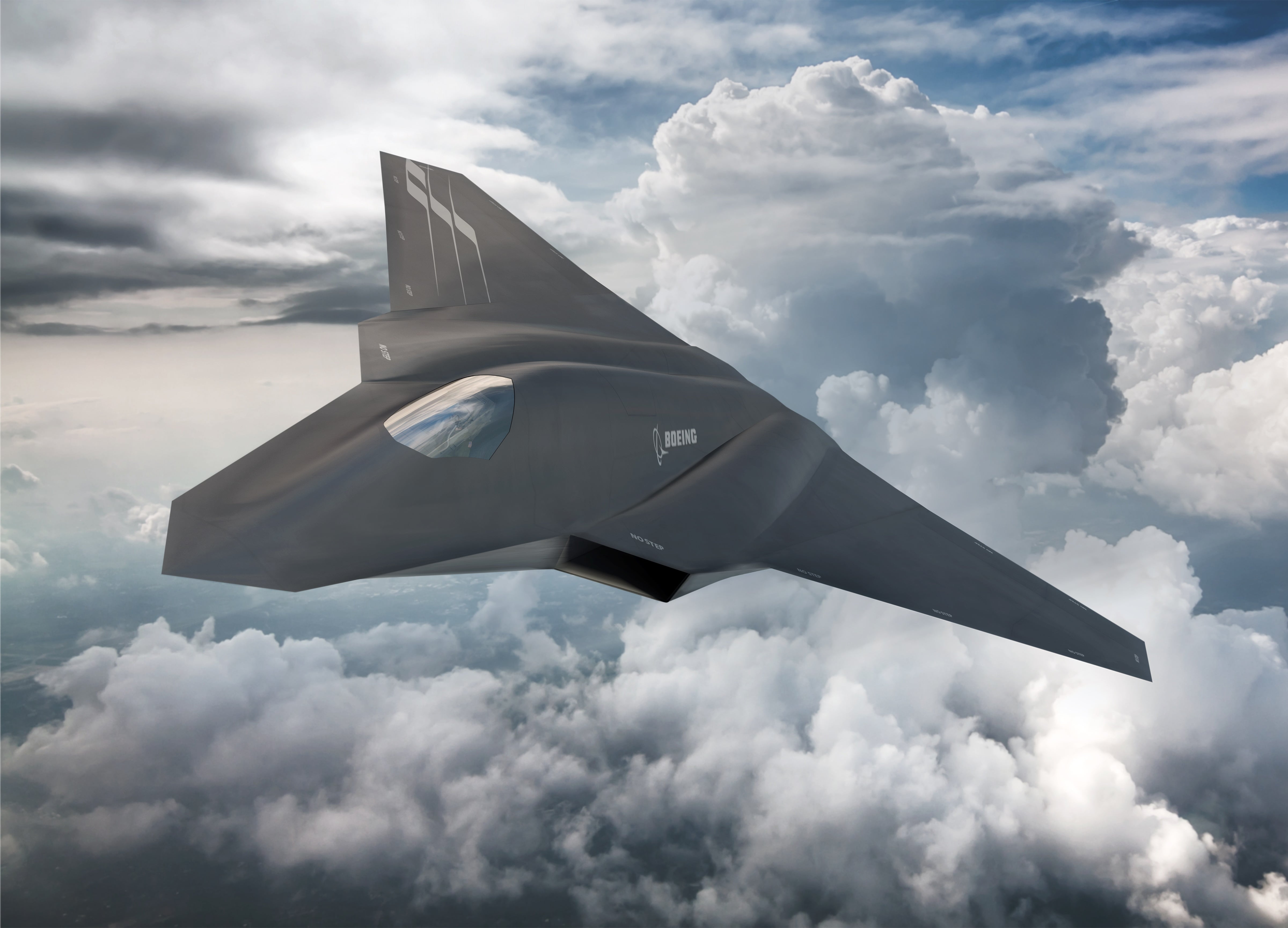
“All of that predated the digital environment,” he explained. “There really hasn’t been a requirement that’s out there for [digital engine designers] to really sink their teeth into until we got to NGAD.”
Having the propulsion system digitally designed and built, from the ground up, will make it easier to update and further develop at pace with evolving threats, Sneden added.
NGAP is still in the early design stages, he said, but as it moves into the testing phase, the digital-based modeling will help fine-tune digital tests and combine various models to see the second- and third-order effects of design changes.
“When you start getting into testing models, you might have one that’s different for structures, you may have another one that’s different for thermodynamic properties of the engines,” Sneden explained. “Can we pour those together so we can better see, when you make a change here, here’s how it impacts you downstream?”
When the time comes to start prototyping or building the engines, he added, the contractors can send 3D digital blueprints to their own suppliers to make components, instead of relying on 2D drawings.
‘Physics gets a vote’
Penney stressed that for digital engineering to yield benefits, a program must take the time and effort from the start to understand exactly how it will use digital tools.
“If you don’t have that foundation, that will leave you with technical debt as you begin to move forward,” Penney said, and could inadvertently cause problems further on down the road. “You have to get it right at the beginning.”
In Dayton, officials agreed with Kendall’s comments that advancements in digital modeling — while important — can’t entirely replace real-world testing. They described how they hope future programs can use both techniques to fill in the gaps a single approach would provide.
The Air Force, along with GE Aerospace and Pratt & Whitney, already conducted a great deal of design and development on adaptive engines that were considered as replacements for the F-35 under the Adaptive Engine Transition Program, or AETP.
The Pentagon ultimately decided not to put AETP in the F-35, instead opting for an upgrade of the fighter’s current engines. But AETP engine technology — such as the adaptive fans that will allow the engine to shift to the most efficient configuration for a given situation — will likely be folded into NGAD’s engine development process.
Sneden said by leveraging existing AETP technology, NGAP can reap the best of both worlds when it comes to testing. NGAP will use digital modeling, he explained, but those digital tests will be shaped by real-world results from prior tests conducted for AETP.
“When we’re testing an engine, we’re actually testing a series of technologies to find out how they work so you can actually craft a testing baseline,” Sneden said. “We’ve done real-world testing [on the XA100 and XA101 engines] so we can see how adaptive engine technology runs across the portfolio, how those materials hold up, how the adaptive fan works — all of that.
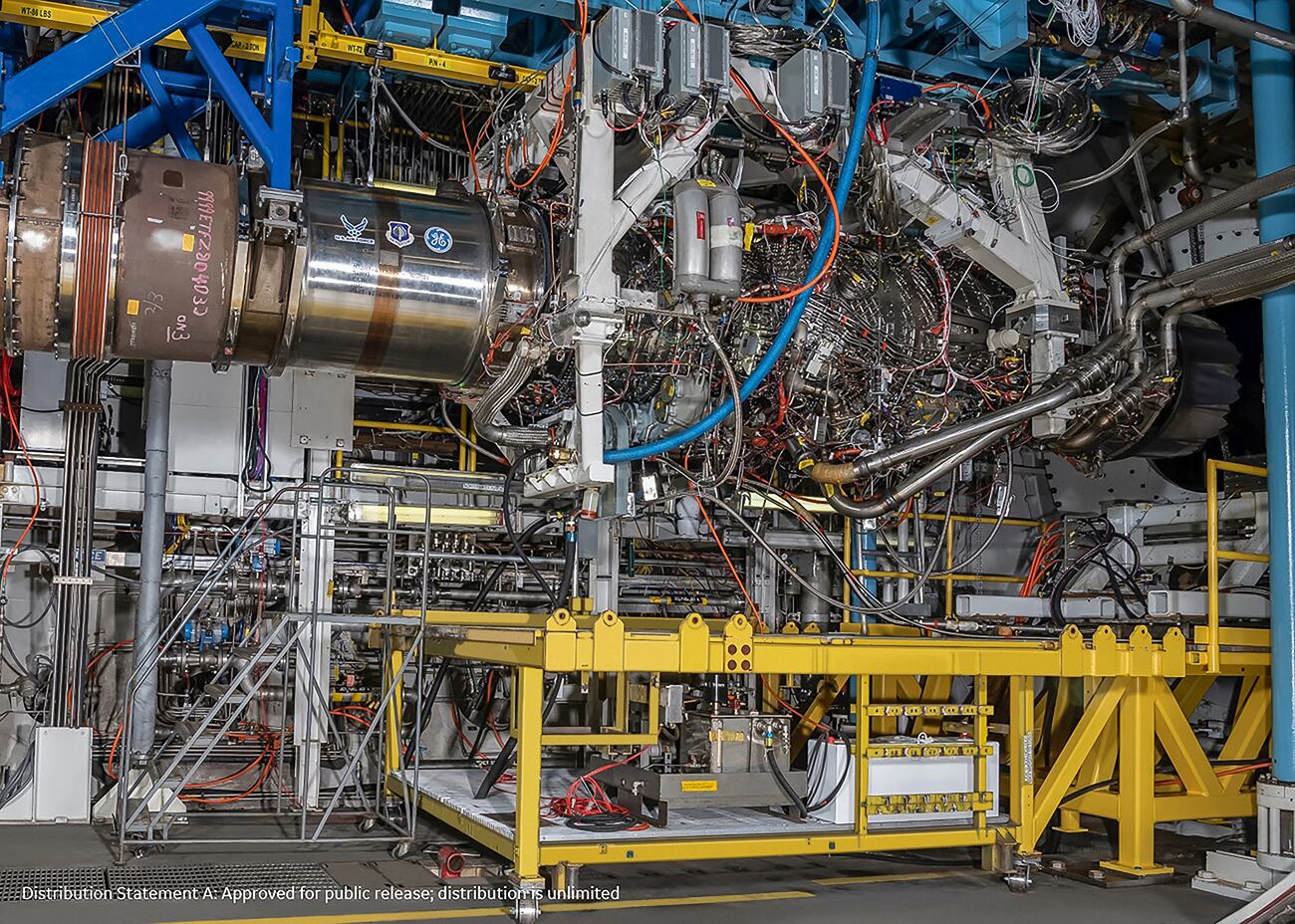
“Now what you can do is take that testing baseline and start incorporating it into your NGAP understanding, and start to merge those worlds of ‘real world’ and ‘digital’ together so you have this nice fusion that happens.”
White, in his own roundtable, underscored the Air Force’s intent to use digital testing to buttress real-world testing. His office hopes that combining the two forms of testing will allow it to cover gaps and yield a much richer set of data.
“We’re using the virtual aspects of the model to make sure that we’re filling in the blanks of the data,” White said. “And then as you do that, it’s kind of like a puzzle. The puzzle starts to fill its way out, and you become more comfortable.”
Having multiple ways to conduct testing comes in handy when trying to put fledgling aircraft through some of the more extreme flying conditions they might encounter, said Col. Kirt Cassell, chief of the Air Force’s T-7 Red Hawk program office.
“No matter how good your digital engineering is, physics gets a vote,” Cassell said. “When you’re at high angles of attack ... it’s still very difficult to get advanced models” to predict the real-world physics.
Sneden noted the Air Force hasn’t even begun to reach the limits of how digital tools can help keep an engine running throughout its entire life.
For example, he said, digital tools could help find ways to make spare parts for an engine more easily or efficiently with additive manufacturing. Or it could help find a new way to repair a broken part instead of taking the lengthy and expensive step of replacing it with an entirely new one, he said.
“We’re just starting to lean into that technology,” he added.
Stephen Losey is the air warfare reporter for Defense News. He previously covered leadership and personnel issues at Air Force Times, and the Pentagon, special operations and air warfare at Military.com. He has traveled to the Middle East to cover U.S. Air Force operations.